Brillo Desigual
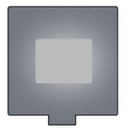
La superficie de la pieza moldeada muestra distintos niveles de brillo en diferentes áreas, aunque el acabado
sea el mismo. Primero la intensidad del brillo depende de la calidad del acabado en la molde. En caso de superficies texturizadas, un buen diseño de molde produce partes con una apariencia más mate, haciendo la reflexión de los rayos de luz difusa y que disimule las irregularidades. Este es un fenómeno en el cual el brillo de la superficie del producto moldeado es parcialmente. Este defecto ocurre cuando la temperatura del molde es baja, cuando el pulido del molde no es bueno y cuando el molde libera muchos agentes usados.
Opaco
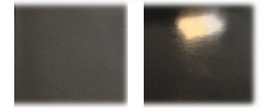
Este es un fenómeno en el cual el brillo de la superficie no es suficientemente bueno. Algunas veces esto es causado por la descomposición del material moldeado, sin embargo, en algunos casos esto es causado también por el uso excesivo de agente desmoldante e insuficiente pulido del molde.
Manchas en forma de halo que se forman normalmente en el área del punto de inyección; a veces también se forman detrás de las transiciones de la sección transversal. La causa de esto, son los esfuerzos de cizalla en estas áreas y la poca adherencia del plástico a la pared del molde debido a las transiciones de la sección transversal. Optimizar la velocidad de inyección, usar un perfil graduado (lento-rápido) y aumentar la temperatura de la masa fundida.
Causas
- Un cambios repentinos en el espesor de pared causados por costillas o postes de montaje puede cambiar el brillo, como los rechupes
- Variaciones de brillo visibles en el área de las líneas de unión debidas, al cambios en la orientación de la masa fundida y al cambio en las condiciones del flujo
- Otro parametros que afectan el brillo son la temperatura del molde, de la masa fundida y la velocidad de inyección, al igual que el punto de conmutación no han sido elegidos correctamente
- El valor y tiempo de la presión de sostenimiento son inadecuados
- Pobre homogeneidad de la masa fundida debido a condiciones de proceso desfavorables
Solución
- Aumentar la temperatura del molde
- Aumentar la temperatura de la masa fundida
- Optimizar la velocidad de inyección
- Ajustar el punto de conmutación a un 94-97% del llenado del molde
- Aumentar la presión de sostenimiento
- Verificar que el tiempo de sostenimiento sea el suficiente hasta que congele el punto de inyección
- Realizar la cuerva tiempo-presión, peso para un mejor ajuste
- Aumentar la contra presión y/o la velocidad del husillo.